
Understanding Calibration and Trimming Marks
Ensuring high standards in any manufacturing process involves multiple layers of checks and balances. Two critical elements in this procedure are the calibration and trimming marks. These small but significant features play a paramount role in maintaining quality control.
Definition and Purpose
Explanation of Calibration Marks
Calibration marks are precise indicators applied during the manufacturing stage. They act as reference points that ensure all subsequent measurements remain uniform. Their primary role is aligning machinery and tools to set dimensions, thereby guaranteeing consistent production output.
Explanation of Trimming Marks
Trimming marks, on the other hand, serve as guides for refining products post-production. These indicators help manufacturers cut materials precisely without compromising their design integrity. They are crucial in practices where exact material removal can translate into superior final products.
Historical Context
The concept of quality control is not new; it has evolved dramatically over the years. Early methods relied heavily on manual inspections with rudimentary tools. However, as industrial needs grew more complex, so did the mechanisms for ensuring accuracy. Modern advancements now enable automated marking techniques, offering unprecedented levels of precision and efficiency.
The Role in Quality Control
Ensuring Precision and Accuracy
How Calibration Marks Contribute to Precision
Calibration marks hold indispensable value by contributing to the precise alignment of production equipment. Consider the automotive industry, where even a slight misalignment could lead to catastrophic failures. Calibration marks ensure each component meets stringent specifications, resulting in safe and reliable vehicles.
Importance of Trimming Marks for Accurate Dimensions
Industries like healthcare benefit enormously from trimming marks. For instance, medical device manufacturers rely on these marks to guide the meticulous processing of surgical instruments. Such precision is vital for devices that must meet rigorous health and safety standards.
Compliance with Standards
Regulatory Requirements
Various industries have strict regulatory requirements governing quality control. Whether it's ISO guidelines or sector-specific regulations such as FDA mandates for medical devices, meeting these standards is non-negotiable. Calibration and trimming marks assist companies in sticking closely to these rules, thereby avoiding costly penalties and recalls.
How Marks Help in Meeting Regulations
.For example, electronics manufacturers might follow IPC standards requiring specific alignments and cuts. Properly placed calibration and trimming marks make it easier for these businesses to comply effortlessly, ensuring consistency while mitigating compliance risks.
Facilitating Troubleshooting and Maintenance
Quick Diagnostics
Effective diagnostics often hinge upon spotting abnormalities quickly. When issues arise, technicians utilize calibration and trimming marks to identify faults swiftly. By examining these reference points, they can easily determine deviations from standard measurements, making problem-solving straightforward.
Simplifying Repairs
During maintenance routines, these marks prove invaluable. Components marked accurately simplify replacement and adjustment tasks. Technicians save time and avoid errors, ultimately extending the lifespan of machinery and reducing downtime.
Impact on Product Integrity
Consistency in Production
Role in Mass Production
Quality control becomes exponentially challenging as production scales up. Calibration and trimming marks offer a robust solution by ensuring every unit matches predefined criteria. This level of consistency is particularly beneficial in sectors like textiles, where vast quantities need uniformly high standards.
Case Studies on Improved Consistency
Consider a clothing brand utilizing Yiwu Jinyao's calibrated woven labels. Through accurate placement and cutting guided by these marks, the brand ensures that garments are consistent in size and appearance. The end result is a lineup of apparel products that reliably meet customer expectations, batch after batch.
Customer Satisfaction
Enhanced Product Reliability
Reliable products create happy customers. Calibration and trimming marks contribute significantly to producing dependable items, fostering brand loyalty. Enhanced reliability means fewer returns and complaints, directly impacting the bottom line positively.
Building Trust with Consumers
Testimonials from satisfied customers often highlight trust built through high-quality products. Brands leveraging these marking methods frequently receive glowing reviews, which act as free endorsements enhancing reputation and credibility.
Technological Integration
Advanced Marking Techniques
Laser Marking
Advances such as laser marking have revolutionized how calibration and trimming marks are applied. Laser offers unmatched precision and durability, making these marks resistant to wear and tear. This technology finds its place in high-stakes environments, ensuring long-term adherence to specified parameters.
Digital Calibration
The advent of smart manufacturing introduces digital calibration integrated with IoT systems. This allows real-time adjustments based on continuous data streams, amplifying operational efficiency and quality assurance dynamically.
Data Analytics and Monitoring
Real-time Data Collection
Incorporating advanced analytics, manufacturers can monitor processes continuously. Real-time data collected from digitally calibrated machines provide actionable insights, facilitating prompt intervention if discrepancies appear.
Predictive Maintenance
Combining predictive analytics with these traditional markings elevates quality control. Predictive maintenance leverages historical and real-time data to foresee potential failures, allowing preemptive actions to maintain optimum production quality.
Practical Applications
Case Studies Across Industries
Automotive
The automotive industry dramatically benefits from calibrations marks, which assure components' fitting and performance, directly impacting vehicle safety and functionality. Routine inspections involve these marks to validate conformance to safety norms.
Healthcare
Medical device fabrication requires pinpoint accuracy, guaranteed by trimming marks. Devices ranging from hypoallergenic needles to intricate surgical robots employ these marks to achieve perfect tailoring, ensuring patient safety.
Electronics
Evolving miniature circuits demand exceptional precision. Electronic gadgets integrate extensive use of both types of marks, preserving the structural integrity throughout mass and intricate productions.
Best Practices for Implementation
Effective implementation starts with understanding your industry's best marking strategies. Employing optimal tools tailored for specific materials and performing regular audits ensure lasting effectiveness.
Overcoming challenges involves adopting versatile solutions addressing variances in marking medium compatibility and underlying manufacturing intricacies.
Future Trends
Innovations in Calibration and Trimming
Emerging technologies promise groundbreaking improvements in these markers, combining nanotechnology advancements for microscopic implementations applicable to novel microfabrication domains.
Impact of Automation
AI and robotic automation mark an evolutionary leap, streamlining marker applications with peerless swiftness and error-margin reduction, forging next-gen benchmarks within the realm of quality assurance.
Final Thoughts
Key Takeaways
The importance of calibration and trimming marks in quality control cannot be overstated. They underpin the very fabric of achieving exactness, remaining pivotal across myriad industries spanning mundane to mission-critical applications.
Encouraging Best Practices
Maintaining vigilance toward continual refinement and harnessing innovative methodologies ensures longevity in retaining unparalleled quality assurance. Constant adaptation encapsulates embracing ever-evolving developments to remain at the forefront of excellence.
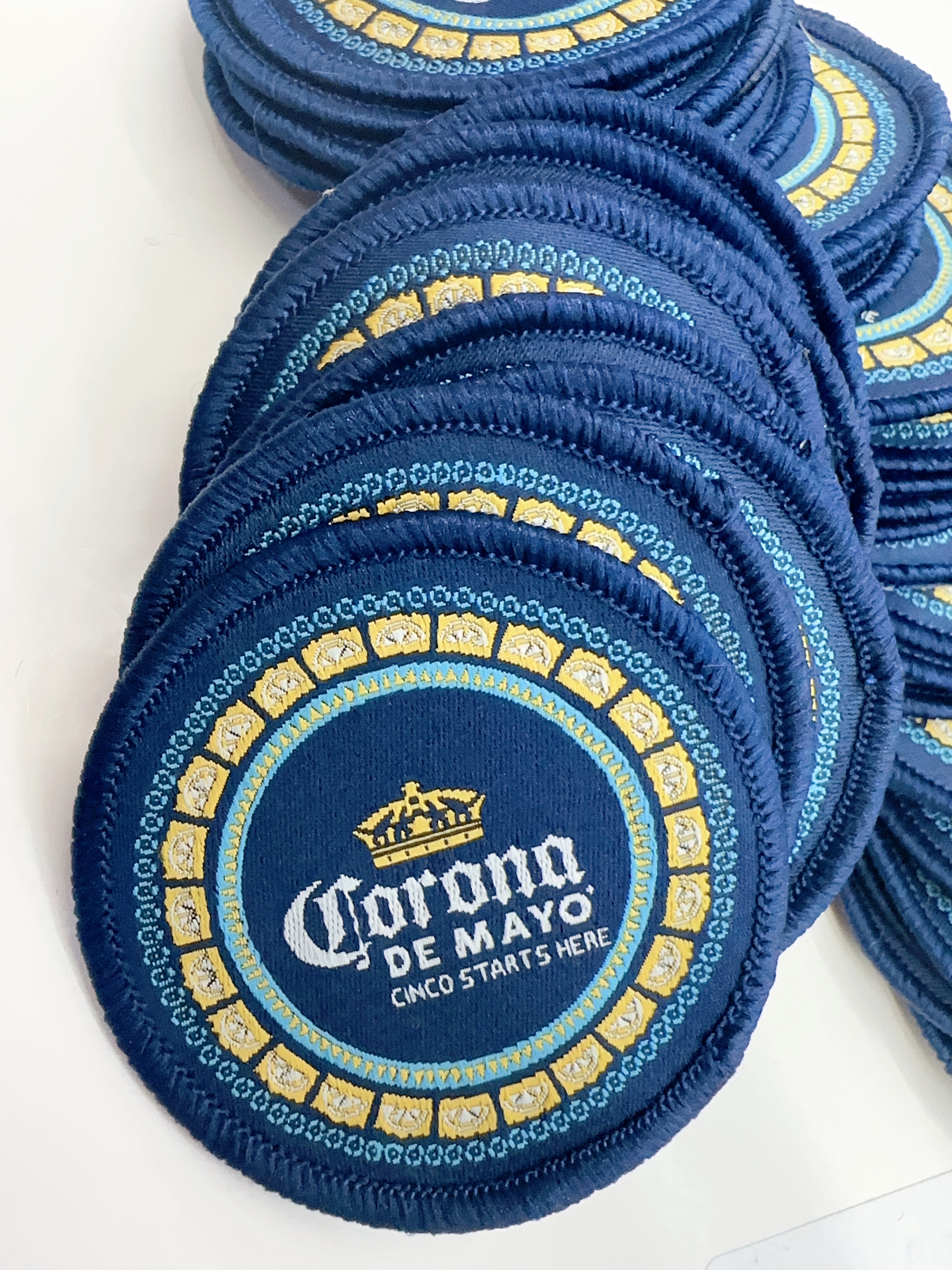